Nitrated welding tables: Negative facts you should know!
The article is based on the scientific research presented in the article ‘Degradation of the nitrided steel layer under the action of welding spatter and electric arc seizures’;
The research was published in the journal Welding Technology Review -. www.pspaw.pl – Vol. 96, 2024, str. 155-160Authors: Aleksander Orłowicz1, Dariusz Pająk2, Paulina Sobolewska3, Tomasz Galek4
You can view the original article in Polish and its English translation at the end of this article.
Does nitriding welding tables make sense? The results of the research are clear.
Nitriding is a process that is theorised to improve the hardness and wear resistance of steel surfaces. For this reason, some manufacturers have started to apply this method to welding tables, hoping to make them last longer. However, recent studies show that in practice, nitriding of welding tables is not only inefficient and costly, but even detrimental to the durability of the welding table surface.
Why would nitriding work?
Nitriding involves the introduction of nitrogen into steel surfaces to increase their hardness. The process seemed attractive to companies who wanted to make welding tables more resistant to chipping and damage. The problem, however, is that despite the theoretical advantages, nitrided coating does not work well in practice under welding conditions, as high temperatures are detrimental to it..
What does the research say?
Tests show that the nitrided surface, despite its greater hardness, is very brittle when exposed to hot spatter and the electric arc. When exposed to heat, the layer quickly cracks and peels, damaging the welding table. The key problem is that the nitriding penetrates the top layer of the material and fills it to such a density that it prevents proper thermal expansion. The result is cracks due to the high temperature, as the material cannot expand properly. This can be explained by a local rapid increase in the value of the linear thermal expansion coefficient in the area where, according to the literature, compressive stresses are already present. This results in complete degradation of the nitrided layer. Such a table will only work well for operations that do not introduce heat into the top layer of the table.
Figure 2 shows a comparison between nitrided and non-nitrided surfaces after exposure to welding spatter. It can clearly be seen that the nitrided surface, despite its theoretical hardness, suffers significantly more damage. (Drawings provided from article, page 157)
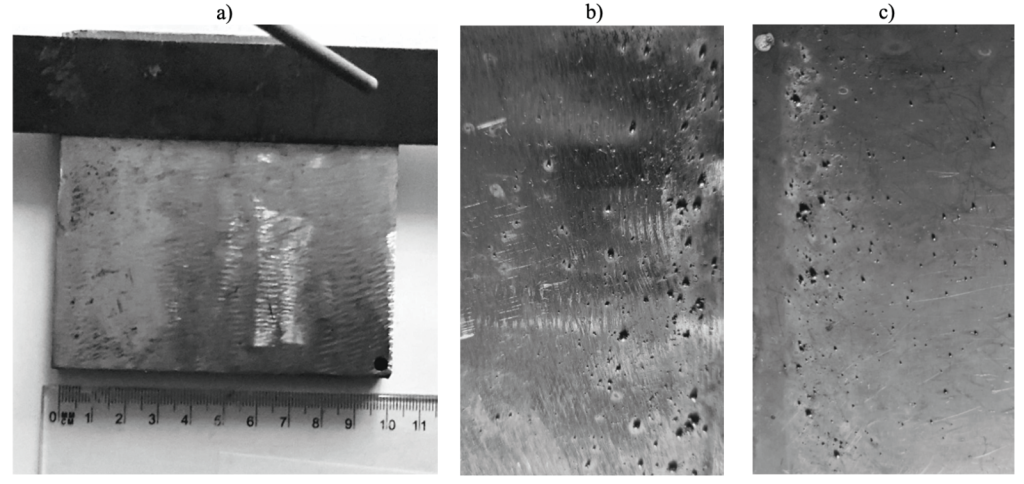
The figures below (Fig. 4 and Fig. 5) show the effects of welding spatter on the nitrided surface, where clear cracking and crumbling and peeling of the layer can be seen. (Drawings provided from article, page 158)
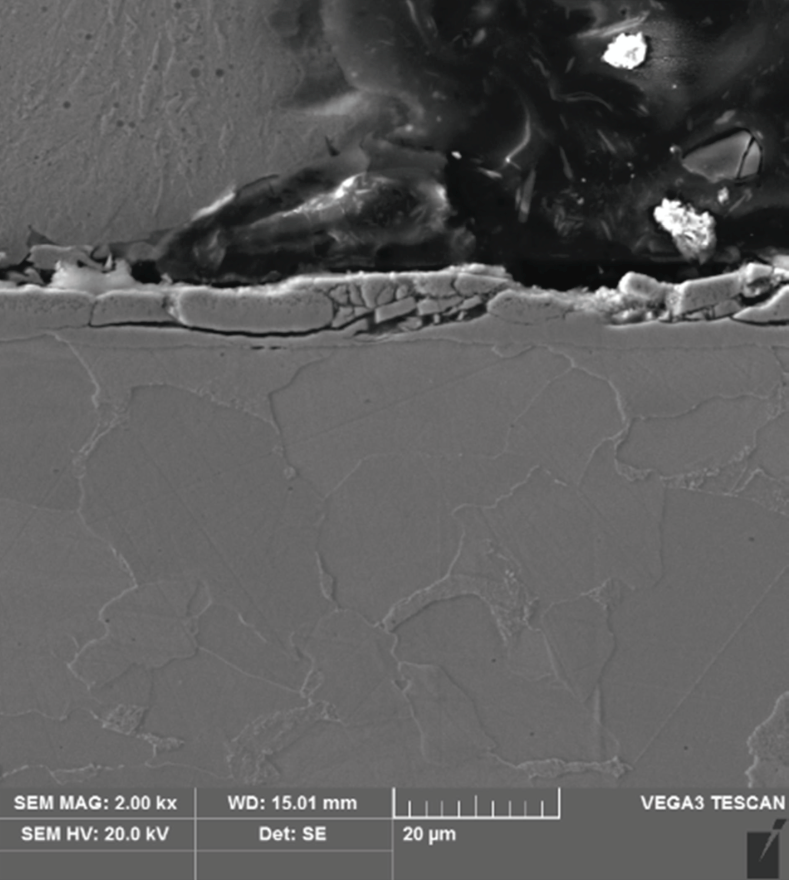

Studies have shown that welding spatter has a temperature that causes thenitrided surface to degrade rapidly. In turn, the electric arc causes the nitrides to break down, making the hard surface become porous and fail to perform its function.
As the figures (Figure 6 and Figure 7) show, the action of the arc causes the nitrides to break down and form a porous, damaged surface. (Drawings provided from article, page 159)
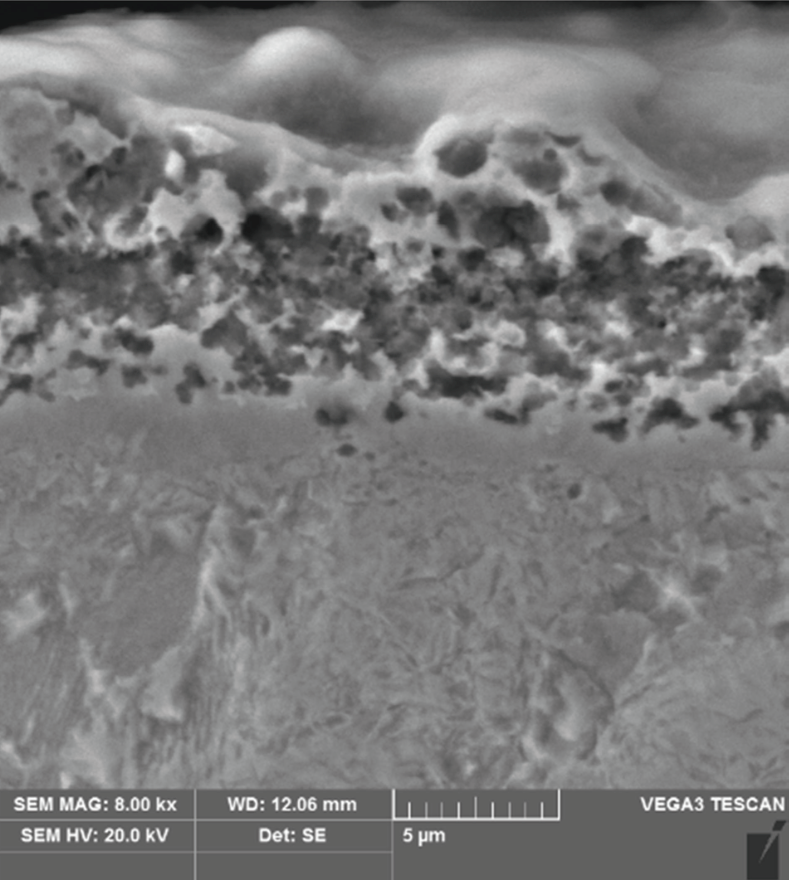
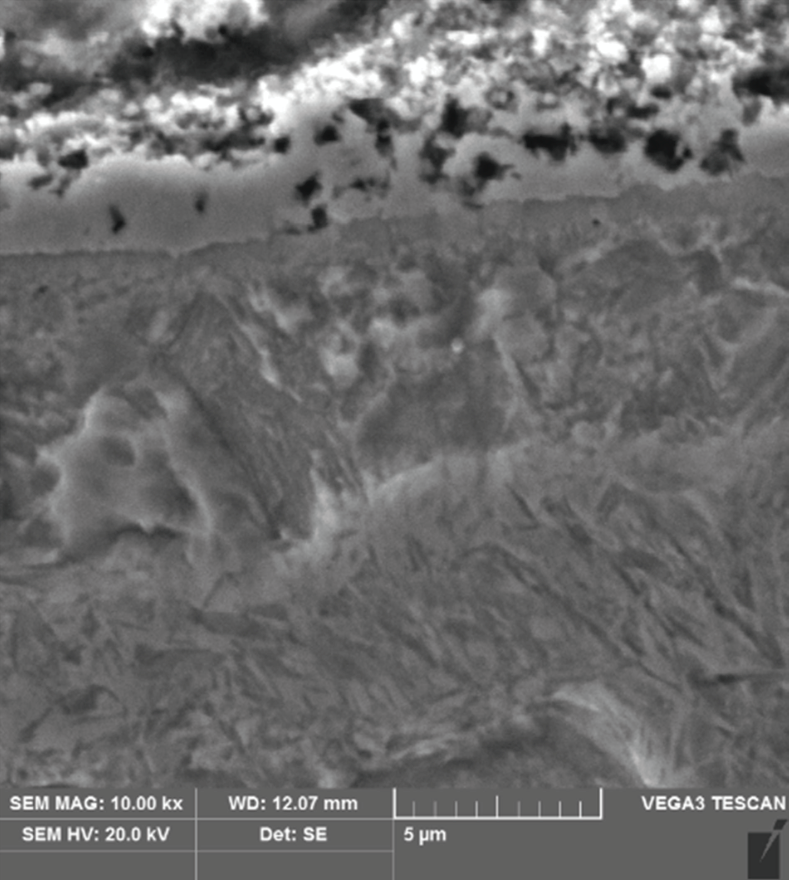
Nitrided welding tables - more problems than benefits.
Although nitriding seems sensible at first glance, in practice the nitrided layer is too brittle to withstand the harsh welding conditions. Instead of protecting the table, it cracks due to heat and spatter.
The nitrided layer does not make the welding tables resistant to the degrading effects of welding spatter and seizures. As a result of the thermal effects of liquid metal droplets, transverse cracks, longitudinal cracks and delamination form in the nitrided layer. In the process of splatter removal, fragments of the nitrided layer are peeled off from areas where it has degraded.
Conclusions for customers
If you want a durable welding table, it is better to avoid nitrided models. Although this process promises hardness and resilience, in reality these tables quickly deteriorate under welding. Instead of overpaying for nitriding, it is worth investing in robust welding tables without this layer. Tables made of durable steel, without unnecessary additional coatings, will perform better in tough welding conditions and are more resistant to heat and damage. The only way to prevent spatters from sticking is to use a proven anti-spatter chemical.
- mgr inż. Aleksander Orłowicz, alekorlowicz[at]gmail.com ↩︎
- Rzeszow University of Technology, Poland; mgr inż. Dariusz Pająk, pajak[at]prz.edu.pl ↩︎
- Rzeszow University of Technology, Poland; dr inż. Tomasz Galek, t.galek[at]prz.edu.pl ↩︎
- Rzeszow University of Technology, Poland; dr inż. Paulina Sobolewska, psobolew[at]prz.edu.pl ↩︎